Best practices for applying water-based adhesives
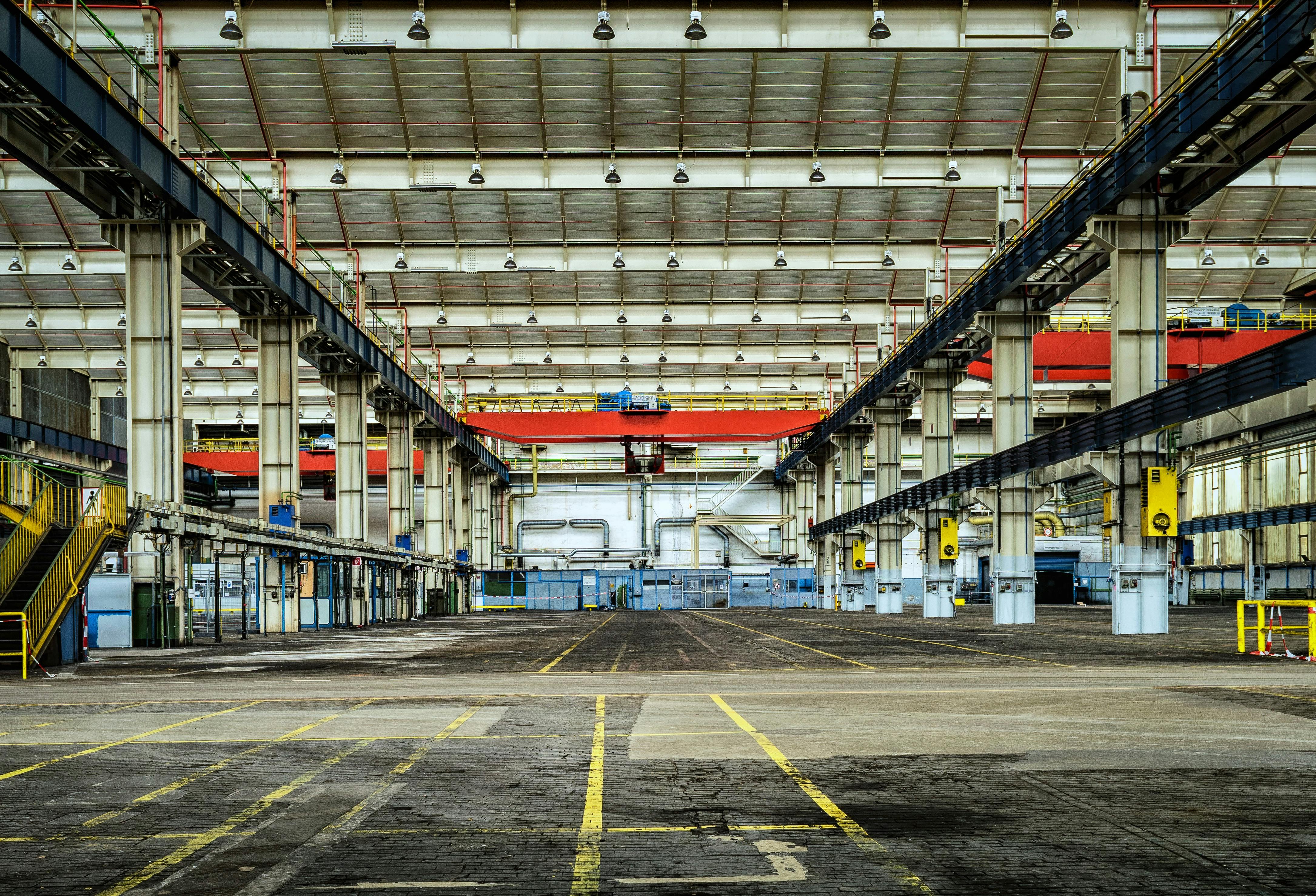
Credit: Pexels
Investing in team training is crucial for maintaining product consistency and quality in the adhesive industry. A well-trained team ensures that water-based adhesives are applied uniformly, reducing defects and improving overall efficiency. Businesses can benefit from structured training programs to elevate their product standards.
Ensuring consistent application of water-based adhesives is more important than ever. Educating your staff becomes a pivotal strategy as you aim to enhance product quality. By establishing clear standard operating procedures and conducting routine skill checks, you can effectively minimize defects and maintain product uniformity. With proper training, your team will be better equipped to handle the complexities of adhesive application, ultimately benefiting your business. To learn more about the benefits of water-based adhesives, you can explore how they contribute to improved product quality.
The importance of staff education
Staff education forms the backbone of any successful adhesive application process. When your team is well-informed about the properties and correct usage of water-based adhesives, it naturally leads to improved performance and fewer errors. Regular training sessions not only keep the knowledge base fresh but also introduce the latest techniques and technologies available in the industry. This continuous learning environment fosters a proactive approach, enabling your staff to anticipate and resolve potential issues before they escalate.
Furthermore, investing in education helps build confidence among your employees. It empowers them to make informed decisions on the job, which can significantly enhance productivity. As each team member becomes proficient in adhesive application techniques, the collective expertise of your workforce grows, contributing to a more efficient production line.
Ultimately, well-educated staff play a crucial role in maintaining high-quality standards and upholding the reputation of your products. By prioritizing education, you not only improve current processes but also pave the way for innovation and advancement within your company.
Implementing clear procedures and routine checks
Implementing clear procedures is essential for achieving uniformity in adhesive application. Standard operating procedures (SOPs) provide your team with a structured framework to follow, ensuring consistency across different shifts and operators. By documenting each step of the process, you minimize variability and reduce the likelihood of errors occurring.
Routine skill assessments further enhance this consistency by identifying areas where additional training might be needed. These evaluations help you pinpoint individual strengths and weaknesses within your team, allowing for targeted improvements. Regular check-ins also serve as an opportunity to address any emerging challenges or changes in production requirements.
Adopting such systematic approaches not only boosts efficiency but also reinforces a culture of accountability among your employees. When everyone adheres to well-defined guidelines, it becomes easier to track performance metrics and implement corrective actions swiftly if needed.
Optimizing training strategies for better outcomes
To maximize the benefits of training initiatives, consider customizing programs according to specific roles within your team. Tailored training ensures that each member receives relevant instruction aligned with their responsibilities, leading to a more competent workforce overall.
Incorporating hands-on practice sessions can greatly enhance comprehension and retention of new skills. Providing real-world scenarios allows employees to apply their knowledge practically while receiving immediate feedback from supervisors or mentors.
Additionally, leveraging digital tools like e-learning platforms can offer flexibility in scheduling training sessions without disrupting daily operations significantly. These resources enable continuous learning opportunities at convenient times for both management and staff alike.